How to Close the Distance with Strangers in One Sentence: "The market is not booming now, there are no orders, do you have any?" This is what the author saw and heard at an electronics exhibition recently. Starting with this, several strangers quickly exchanged contact information and engaged in a heated discussion.
Currently, the global semiconductor industry's downturn has become an undeniable fact. Layoffs, order cuts, and capital reduction, various cost-saving measures are emerging endlessly. Even the leading foundry TSMC has reported a large-scale order cut by customers, with the 7nm process capacity utilization rate falling below 50%. However, in this downturn, the photomask, which is essential for chip manufacturing, has been reported to be in short supply, and prices are expected to rise by 10% to 25% next year.
Advertisement
In the down cycle, who is grabbing the photomask? What is the global market situation?
Down cycle, counter-traveling MASK
The importance of lithography machines in chip manufacturing is well known, and the photomask is the graphic master plate used in the lithography process of microelectronics manufacturing. The photomask, also known as a reticle, photomask, or lithographic mask, is made by manufacturers through lithographic plate-making processes to engrave circuit diagrams on the substrate. The main function is to use the designed pattern to copy the circuit pattern through light transmission and non-transmission, thereby achieving batch production of chips.
From the data, the shortage of photomask supply is not groundless. Public information shows that the delivery time for high-specification photomasks used to be 7 days, but now it has been extended by 4 to 7 times to 30 to 50 days, and the delivery time for low-specification products has also doubled. Some chip design manufacturers even worry that 30 to 45 photomasks are needed for semiconductor development, but they cannot be obtained correctly now. Semiconductor manufacturers reveal that the delivery of manufacturing equipment such as photomask electron beam patterning lighters is delayed, delaying the factory delivery of photomasks and raising product prices.
So, why is the demand for photomasks so high? This needs to be explained from the nature of the photomask. In chip manufacturing, the photomask is an indispensable consumable. Since each photomask can only draw a limited circuit diagram, and chip manufacturing requires many different circuit patterns, many photomasks will be needed accordingly. Especially as chip process technology evolves, the circuit diagrams become more and more complex, and the number of photomasks required also increases. ASML data shows that in 2021, the average number of photomask layers per wafer for the 5nm process was more than 10 layers, and after 3nm, the average number of photomask layers per wafer will double to about 20 layers. In the DRAM part, about 5 layers of photomasks are currently mass-produced using EUV technology, and it will be increased to 8 to 10 layers next year. Although there are many photomasks required per wafer, each photomask will not be used again after the pattern on the plate is transferred, and during the process verification, if there is a design change and the lithographic plate pattern is adjusted, the originally made photomask will no longer be used.
The above attributes determine that the demand for photomasks themselves is very large. However, the reasons why they can still support the counter-traveling market in the down cycle are as follows:
First, the surge in demand for system semiconductors, especially high-performance chips, such as automotive semiconductors and autonomous driving chips, while the expansion of photomask production in the past was very limited.It is well known that the chip market brought by smart cars is very large. Intel CEO Pat Gelsinger predicts that by 2030, the automotive semiconductor market will double to 115 billion US dollars, and the number of semiconductors on high-end cars will increase by 5 times. At present, the automotive field has become a new track for many chip manufacturers, and even storage manufacturers such as Samsung Electronics and SK Hynix have gradually turned their attention to the automotive semiconductor field, let alone other system semiconductor manufacturers, they are flocking in. In the current situation where consumer electronics are losing momentum, cars have become their savior.
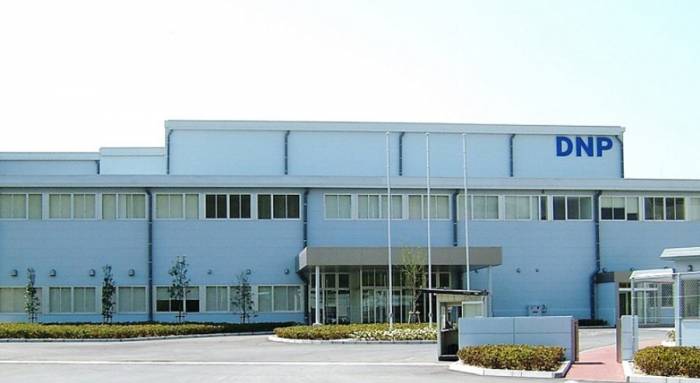
However, the expansion of photomasks in the past was very limited. Generally speaking, photomask manufacturers are divided into two types. One is that foundries such as Intel, Samsung, and TSMC have their own photomask production business, but their production capacity is self-produced and self-sold; the other is third-party photomask manufacturers independent of foundries, such as US Photronics, Japan DNP, Toppan Printing, etc., these manufacturers mainly sell mature process photomasks, such as the aforementioned automotive chips, most of which are still mature processes. McKinsey Senior Consultant Denise Lee recently pointed out that mature process technology will still be the mainstream of automotive chip production, and it is expected that the demand for mature process technology in automotive chips will reach a compound annual growth rate of about 10% by 2030.
Compared with advanced process photomasks, the profit margin of mature process photomasks has been low for a long time. In the next ten years, it will take an investment of 1-2 billion US dollars to update production equipment, let alone build new production lines. Toppan Printing once estimated that, taking the 65-nanometer node as an example, a new photomask production line is expected to require an investment of 65 million US dollars. The huge depreciation cost may be reversed with the current market price of photomasks, and the long-term return on investment is not enough to stimulate manufacturers to invest, which also makes the expansion of photomasks limited in the past. Therefore, facing the current surging demand, the production capacity of photomask factories is inevitably a bit "tight". Under the situation of supply not meeting demand, the market naturally goes against the trend.
The second is that the production capacity of wafer foundries and IC design factories is gradually released, and more new chips complete the design plan, and the photomask case gradually emerges.
Taiwan Photomask General Manager Chen Lidun previously analyzed that the demand for semiconductors is going down, but the production capacity of wafer foundries and design companies has begun to loosen. However, because there is idle production capacity, new chips complete the design plan, and the photomask case can start to flood in, and there are more Tape out coming in. For photomask factories, customer demand has increased, and the demand in the second half of the year is better than in the first half.
The above-mentioned different chip designs require different photomasks. The development of technologies such as autonomous driving, 5G, and the metaverse has created new demands for chips. However, due to the severe shortage of chips before, chip design factories and foundries focused on short chips and had no time to pay attention to too many new demands. Now, the shortage of chips has been significantly alleviated. Although the industry has completely reversed, it is already in a downward cycle, but design manufacturers want to be invincible and seize the future market is still the top priority. With this comes the "rise" of the number of new chip design cases, which is also the reason why IC design factories expand orders for photomask manufacturers. They need to purchase new photomasks and supply them to foundries.
Chip design factories place orders frantically, but the existing production capacity of photomask factories is limited, and expansion also requires time. In the short term, there will be no new production lines, which also exacerbates the tense supply and demand relationship.
The increase in investment by photomask giants
Although photomask manufacturers have been very cautious about expansion in the past, under the current industry situation, the giants are also making big moves, such as the recent Taiwan Photomask. Taiwan Photomask is the world's sixth-largest photomask manufacturer. The latest financial report shows that Taiwan Photomask's consolidated revenue in the third quarter reached 2.068 billion yuan, a year-on-year increase of 28%; the third quarter operating gross profit was 542 million yuan, a year-on-year increase of 48%; the third quarter operating net profit was 305 million yuan, a year-on-year increase of 89%.In order to address the ongoing tight capacity of photomask production and to preemptively secure key production capacity, Taiwan Photomask has decided to increase its capital expenditure by NT$460 million against the trend, to order semiconductor inspection equipment from KLA. It is expected that the equipment will be installed in December this year and will generate revenue in the first quarter of next year, with an estimated revenue growth in double digits. Previously, Taiwan Photomask mainly supplied 6-inch/8-inch wafer foundries, and since 2019, it has further expanded into the 12-inch wafer photomask market. Legal persons estimate that the proportion of 12-inch photomask business of Taiwan Photomask will increase from 21% in 2021 to 30% this year. In addition, Taiwan Photomask's 40nm is expected to be mass-produced in 2022, and 28nm is estimated to be mass-produced in the first half of 2023, while 90/65nm and other process products have already been mass-produced.
As early as early March this year, Taiwan Photomask held a board meeting to issue new shares through cash capital increase, and planned to raise NT$6 billion through cash capital increase within two years to support the construction of factories and the purchase of machinery and equipment, as the funds needed for the medium and long-term capacity upgrade plan. After the completion of the plan, it is expected to increase the capacity by 20% and support the photomask required for the semiconductor process up to 40nm. At that time, the news showed that in addition to expanding production in the existing plant area, Taiwan Photomask will also invest in building a new factory in the Tongluo Industrial Park in Miaoli. In early January this year, Taiwan Photomask also announced an investment of NT$3.557 billion, mainly for capital expenditure on capacity expansion and factory construction.
As a key material in chip manufacturing, the strength of Japan, a major semiconductor material country, is naturally not to be underestimated, with several giant companies such as SKE, Hoya, Japan DNP Printing Co., Ltd. (Dai Nippon Printing), and Toppan Printing Co., Ltd. In August this year, Nikkei News reported that due to the optimistic outlook for the strong demand for semiconductors in the medium and long term, the major Japanese semiconductor material company Toppan Printing will invest about 20 billion yen (about RMB 1.013 billion) through its subsidiary "Toppan Photomask" before the fiscal year 2023 to expand the photomask production capacity of factories in Japan and Taiwan.
Toppan Photomask is a subsidiary established by Toppan Printing in April this year to separate its photomask business, in order to facilitate the collection of investment funds from the outside. It is reported that Toppan Photomask will add a production line for photomasks used in advanced products such as 5-10nm logic chips and 10nm grade DRAM. The production capacity of advanced process products will increase by about 20% compared to the fiscal year 2020. Toppan Printing pointed out that it is not surprising that the excess situation in the short term will be resolved, but the demand will grow in the medium and long term.
In addition, Nikkei News reported in February that DNP will invest nearly 10 billion yen in production plants in Japan, mainland China, and Taiwan before the fiscal year 2023 to increase production lines. It is understood that DNP has established joint ventures with local companies in Taiwan, mainland China, and Italy, and will increase production capacity in the future through capital increases and other methods, to build a production system that can deliver in the short term according to supply and demand. DNP stated that there is a shortage of photomasks used for mid-range products with high versatility such as automotive and sensors, so it has decided to increase production.
It is worth mentioning that on November 10, DSP announced that it will invest 20 billion yen to build a large metal photomask production line at the Kurosaki factory in Kitakyushu, Fukuoka Prefecture, and is expected to start operation in the first half of 2024. Although this production line is mainly used for manufacturing photomasks required for OLED displays, not for chip manufacturing, it also reflects to some extent that the demand for photomasks is very strong, whether it is display or chips.
Closely following domestic manufacturers
Affected by the improvement of the overall market sentiment of photomasks, the recent stock prices of China's two major photomask manufacturers have also increased against the trend. On November 10, Luwei Photoelectric's stock price rose by more than 10%, and Qingyi Photoelectric's stock price rose by more than 7%, and the financial report data of the two companies are even more pleasing. Among them, the leading manufacturer Luwei Photoelectric's single-quarter operating income in the third quarter was 199 million yuan, a year-on-year increase of 31.21%, and the net profit attributable to the parent company was 39.0537 million yuan, a year-on-year increase of 104.74%; Qingyi Photoelectric's total operating income in the third quarter was 206 million yuan, a year-on-year increase of 28.95%, and the net profit attributable to the parent company in this quarter was 30.1541 million yuan, a year-on-year increase of 193.82%.
Although the net profit growth rate has soared, it should be noted that the main business of the two giants is in the flat panel display field, and the proportion of semiconductor chip business is less than 20% (Luwei Photoelectric's semiconductor chip business accounted for 19.68% in 2021, and Qingyi Photoelectric's semiconductor chip business accounted for 16.68% in 2021). However, fortunately, with the increasing voice of downstream wafer factories, the pace of domestic substitution is expected to accelerate, and the capabilities of domestic photomask manufacturers are also continuously growing.Luwei Optoelectronics plans to raise 405 million yuan in its IPO this year, mainly for the expansion of high-precision semiconductor photomask production and large-size flat panel display photomask production projects. Luwei Optoelectronics stated that the fundraising projects will further enhance the mass production capacity of semiconductor photomasks to the 130nm process node, and based on independent research and development, break through key technologies such as precision control and defect control in the manufacturing of semiconductor photomasks, further advancing the manufacturing technology of semiconductor photomasks to process nodes such as 110nm/90nm/65nm. It is reported that Luwei Optoelectronics has achieved mass production of semiconductor photomasks at the 250nm process node, and has mastered the core technology capabilities for manufacturing semiconductor photomasks at the 180nm/150nm process nodes.
Qingyi Optoelectronics is also accelerating the layout of semiconductor chip photomasks. It has achieved mass production of 6-inch and 8-inch semiconductor chip photomasks at the 250nm process node, and is promoting customer testing and certification of 180nm semiconductor chip photomasks. At the same time, it is carrying out process research and development of 130nm-65nm semiconductor chip photomasks and planning the process development of photomasks required for 28nm semiconductor chips.
In addition, in order to further meet production capacity, Qingyi Optoelectronics is actively introducing the necessary equipment. The newly introduced semiconductor chip photomask lithography machine and supporting equipment at the Shenzhen factory have been put into production, increasing the production capacity of products such as semiconductor chips, MicroLED displays, and silicon-based semiconductor display photomasks. According to the financial report data of Qingyi Optoelectronics last year, the semiconductor chip field has become the fastest-growing business, with a growth rate of up to 39.42%, and is expected to become a new incremental business.
While domestic manufacturers are making efforts, semiconductor giants are also actively building photomask factories. The Qingdao Xin'en project, which is deeply involved by "the father of Chinese semiconductors" Zhang Rujing, has built its own photomask factory. In August 2021, Qingdao Xin'en officially announced the successful production of 8-inch factories, with the production of power chips, and the yield rate is above 90%. The photomask factory also completed product delivery at the same period. In August this year, the photomask material industry chain project led by Zhang Rujing was signed and settled in Jiaxing, Zhejiang, with a total investment of 3 billion yuan, and the first phase of investment is 1.1 billion yuan, mainly engaged in the research and development of photomask material industry chain-related products.
In conclusion, the counter-trend expansion of photomask manufacturers and the large silicon wafer manufacturers have a "similar charm" in a certain sense, both of which are looking at the long-term strong demand for semiconductors. Data from DigitalJournal shows that the global semiconductor photomask market size was 4.687 billion US dollars in 2021, and is expected to grow at a compound annual growth rate of 6.11% during the forecast period, reaching 6.6912 billion US dollars by 2027. Compared with the trillion-dollar market of the integrated circuit industry, this data can be said to be negligible, but the photomask has an important role in the entire industry. The quality of the photomask can directly affect the quality of photolithography, and then affect the performance of the chip.
According to the report from Minmetals Securities, there are three main development trends of photomasks in the future: First, the precision tends to be refined. In the semiconductor field, the evolution of advanced process technologies has put forward higher requirements for the corresponding wafer manufacturing and chip packaging photomasks. With the proportion of advanced processes expected to increase, the precision of photomask products will become more refined in the future; second, the size tends to be large, with the size of televisions becoming larger, driving the panel substrate to gradually become larger, which directly determines the size of the photomask products to become larger; third, the photomask manufacturers extend to the upstream industry chain, in order to reduce the cost of raw material procurement and control the quality of terminal products, photomask manufacturers have begun to extend to the upstream industry chain, and some companies such as HOYA and LG-IT have already had the production capacity of the entire industry chain of photomasks, including grinding/polishing, chrome plating, and photoresist coating.Although domestic photomask manufacturers have made significant progress, the lack of an upstream industrial chain has also hindered their development pace. However, looking at the overall situation, it is still a long and arduous task to penetrate the entire industrial chain, but we must still believe that there will be a dawn ahead.
Comments