Over the past two years, the global shortage of semiconductor chips has become a focal point. On the other hand, the supply chain shocks brought about by the pandemic and unprecedented demand have triggered shortages worldwide and in some key industries, prompting chip giants to take action to prevent and alleviate such shortages. Southeast Asia is becoming the "treasure land" that chip giants are betting on.
Southeast Asia has a unique neutral regional positioning, a comprehensive and diverse semiconductor ecosystem, and is deeply integrated into the global value chain. Counting the countries in Southeast Asia, Singapore's human capital, infrastructure, and friendly business environment make it a natural first choice for docking. The Philippines, Malaysia, Thailand, Vietnam, and Indonesia have skilled labor and talent foundations that can support the back-end manufacturing of complex chips. Southeast Asian countries have ushered in diversified investments from chip giants.
Advertisement
Singapore - A Manufacturing Powerhouse
Singapore is an important semiconductor manufacturing base. It is home to Micron's global operations headquarters, three memory wafer factories, and an assembly and testing facility. It is also the location of Infineon's Asia-Pacific headquarters, responsible for managing key functions including research and development, supply chain, sales, and marketing. At the same time, both GlobalFoundries and UMC have wafer factories in Singapore, producing chips with a process up to 40nm. Large OSAT companies, including ASE and Jiangsu Changdian Technology, also have assembly and testing factories in Singapore.
According to an estimate by the Business Times in July, global chip manufacturers have invested nearly 200 billion US dollars in Singapore to reduce risks and enhance supply chain resilience. The main investments by major factories this year include:
French wafer manufacturer Soitec said in July 2022 that it will invest 400 million euros to expand the scale of its Singapore Pasir Ris factory. By 2026, this supplement will enable Soitec to produce 2 million 300mm wafers, accounting for two-thirds of its global capacity.
The American wafer foundry GlobalFoundries announced an investment of 4 billion US dollars to expand its manufacturing capacity. In June, GlobalFoundries said it had begun moving into its new factory, which is expected to reach full production in early 2024 and increase its capacity in Singapore to 1.5 million 300mm wafers per year.
Taiwan Semiconductor Company, United Microelectronics Corporation, said in February 2022 that it would invest 5 billion US dollars to build a new factory in Singapore to produce 22 and 28-nanometer chips, taking advantage of the demand for 5G and automotive electronic products. The factory is located next to the existing 300mm wafer factory in Pasir Ris, and is expected to have a monthly production capacity of 30,000 wafers when it starts production at the end of 2024.
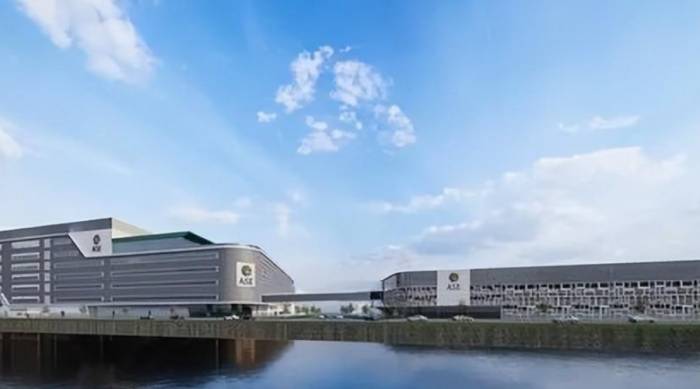
Malaysia - A Major Packaging and Testing Center
Penang, Malaysia, known as the Silicon Valley of the East, has successfully transformed into Malaysia's leading electrical and electronics (E&E) center. According to SEMI data, Penang's global semiconductor industry's back-end output accounts for about 8%, making it a world-leading region for microelectronics assembly, packaging, and testing.On November 10, 2022, ASE Technology Holding Co., Ltd. (Xiang Guang) broke ground for its new chip assembly and testing plant in Penang, Malaysia. The new factory of Advanced Semiconductor Engineering (M) Sdn. Bhd. (ASEM) will include two buildings (Building 4 and Building 5), with a construction area of 982,000 square feet, located in the Bayan Lepas Free Industrial Zone. The core focus of this factory is high-demand packaging product types, including copper clips and image sensors.
In addition to the packaging and testing field, Malaysia also has some major component and power semiconductor manufacturers.
The MLCC giant Taiyo Yuden announced on September 21, 2022, that due to the optimistic outlook for the continued expansion of MLCC demand in the future, it will invest about 18 billion yen to build a new MLCC factory within its subsidiary in Sarawak, Malaysia, "TAIYO YUDEN (SARAWAK) SDN. BHD." The new factory is expected to be completed in March 2023.
Currently, Bosch is building a new semiconductor testing center in Penang, Malaysia. By 2023, the center will be used to test finished semiconductor chips and sensors.
On July 15, 2022, Infineon Technologies held the groundbreaking ceremony for its most advanced wafer factory in Kulim, Malaysia. The factory has an investment of more than 8 billion ringgit and will significantly increase the company's manufacturing capacity for SiC and GaN power semiconductors. It is expected that the factory will be completed in the third quarter of 2024.
Lam Research is the first wafer manufacturing equipment manufacturer to set up a manufacturing plant in Malaysia and is also the company's largest manufacturing plant. The following is a new manufacturing plant built by Lam Research in Batu Kawan, with a construction area of 800,000 square feet and an investment of 1 billion ringgit. According to semianalysis estimates, more than 1/3 of Lam Research's manufacturing capacity in the future will be in Malaysia.
However, with the implementation of capacity expansion and factory construction in Malaysia, a major challenge faced by Malaysia is the shortage of workers. A survey conducted by the Malaysian Semiconductor Industry Association (MSIA) on its 80 members in November 2021 concluded that the industry urgently needs at least 30,000 workers.
Japanese semiconductor manufacturers are taking root in Thailand.
Thailand is the world's 13th largest base for manufacturing electronic products and components. In the printed circuit board (PCB) market, Thailand is the world's seventh-largest exporter. Thailand is particularly "loved" by Japanese semiconductor manufacturers, with Sony, Rohm, Samsung, Murata, Toshiba, Kyocera, and others establishing fabs in Thailand. Thailand is a gathering place for long-term investments by Japanese companies. In addition, NXP Semiconductors, Western Digital, and Microchip Technology also have factories in Thailand.Sony is the world's largest image sensor manufacturer, controlling about half of the market share. On November 13, 2022, Sony Group will invest about 10 billion yen ($70.7 million) to establish a semiconductor factory in the production base in central Thailand. The factory will start operating in the fiscal year ending March 2025, mainly for manufacturing image sensors. Sony currently handles most of the front-end and back-end processes for automotive sensors at its Japanese factory. It now plans to focus on front-end processing in Japan and let its Thai business take over the rest.
Murata is the world's largest capacitor supplier. Capacitors are tiny components that store and release electrical charge in smartphones and other devices. Murata is also a component manufacturing supplier for Apple. On November 14, 2022, Murata announced that it has started building a factory in Thailand to produce capacitors. This is also Murata's first production of MLCC products in Thailand. The new factory, costing 12 billion yen, will be put into operation in October 2023, aiming to balance production between Japan, China, and Southeast Asia. Before this, Murata had a factory in Thailand producing sensors and other electronic devices.
The king of electronic ceramics, Kyocera, announced in November 2021 that the company plans to build a new plant for semiconductor packaging in Vietnam, with an estimated investment scale of about 10 billion yen. The new factory is currently in the detailed design stage and is planned to start operation between the end of 2022 and the beginning of 2023.
Thailand has a large pool of human resources, with 750,000 people currently working in the electronics and electrical industry in Thailand. The government is actively accelerating efforts to improve the skills of the workforce to support rapidly changing technology. Additional tax incentives are also provided to encourage companies to participate in human resource development. Reducing labor costs is a key factor in gaining competitiveness, so doing business in Thailand, where labor costs are relatively low, will be very beneficial.
Previously, Thailand also introduced incentives for semiconductors. The Board of Investment of Thailand (BOI) stated that companies with R&D expenditures of not less than 1% of their total sales or not less than 200 million baht in the first three years will be granted an additional corporate income tax exemption for up to 5 years, depending on the amount of R&D investment. Companies that increase R&D investment in their main business can enjoy a joint tax exemption period of up to 13 years.
Vietnam Becomes a New "Foothold" for the Semiconductor Industry
Vietnam has become the second choice for manufacturing enterprises due to its proximity to China. Vietnam is not a newcomer to the semiconductor industry. The country's first semiconductor factory, Z181, was established in 1979, producing and exporting semiconductor components to the Eastern Bloc during the Cold War. The dissolution of the Soviet Union and the subsequent trade embargo ended the country's first attempt to develop semiconductor capabilities.
However, the desire to enter the global semiconductor value chain still exists. To attract high-tech investment, Vietnam's industrial and technology policies have always given the highest rewards to high-tech projects, including exemptions from corporate income tax and sales tax, as well as exemption from land rent. Vietnam also has one of the most open economies in the world, with 15 free trade agreements. For example, in 2015, Vietnam and South Korea signed the Vietnam-Korea Free Trade Agreement (VKFTA). According to the VKFTA, Vietnam abolished 31 tariff items on electronic products and components imported from South Korea, which also prompted the South Korean semiconductor giant Samsung to build a factory in Vietnam.
Vietnam's advantages over its regional neighbors are also reflected in talent. More than 40% of Vietnamese college graduates major in engineering and technology, and Vietnam has become one of the top 10 countries with the most engineering graduates. Semiconductor companies can have young engineering talent at a relatively low cost.
However, the weaknesses of Vietnam's investment environment lie in the backward infrastructure, weak intellectual property enforcement, cumbersome procedures, underdeveloped supplier networks, and a lack of local skills.Samsung is the world's largest manufacturer of memory chips, producing semiconductors. Samsung has a total of six factories in Thailand, and earlier this year, Samsung invested $920 million in its electronic components factory located in Thai Nguyen. At the end of August 2022, Samsung intends to invest an additional $3.3 billion in Vietnam to continue expanding its business in the country. It is also testing the production of FC-BGA high-performance semiconductor packaging substrates in Thai Nguyen Province in northern Vietnam, with plans to officially start mass production in July 2023. Part of this $3.3 billion investment commitment has already been fulfilled, including $841 million for the Samsung Electronics HCMC CE Complex (SEHC) and $1.187 billion for Samsung Electro-Mechanics (Vietnam) Co., Ltd.
Hana Micron, a South Korean manufacturer, mainly focuses on packaging and testing memory semiconductors, with its main customers being Samsung Electronics and SK Hynix. In November last year, it won orders for DRAM and NAND memory packaging and post-processing testing from SK Hynix. According to industry sources, the contract is worth 1 trillion won and will last until 2027. Due to the significant increase in the number of memory semiconductor packaging and testing by SK Hynix, Hana Micron has decided to increase its workforce in Vietnam to 3,000 people by 2025.
More and more investors are interested in this field in the Vietnamese market. Intel is a typical example. Intel CEO Pat Gelsinger said during a meeting with Vietnamese Prime Minister Pham Minh Chinh in May this year that Vietnam is a vibrant economy with a potential market of nearly 100 million people, making it an attractive destination for investors. Intel invested $1 billion in a chip packaging and testing factory in Vietnam many years ago, and to this day, the factory remains an important production base for the Intel group. In recent meetings with Vietnamese leaders, Intel emphasized that it will expand its investment scale in Vietnam, with an investment amount several times higher than before.
At the end of December 2021, Amkor Technology signed an agreement to establish a $1.6 billion semiconductor manufacturing plant in Bac Ninh Province, home to global manufacturers such as Foxconn, Samsung, and Canon. On Amkor's third-quarter earnings call, the company stated that the factory project in Vietnam is proceeding as planned.
In addition to the aforementioned companies, EDA software giant Synopsys is transferring its investment and engineering training from China to Vietnam. There are also companies like Renesas, Applied Micro, Splendid, and Sonion investing in Vietnam, but the project scales are relatively small.
India Joins the Global Chip Manufacturing Race
As we all know, India has a significant advantage in the field of chip design. Bangalore, India, is one of the world's largest chip design centers and is known as the "Silicon Valley of India."
The expansion of international semiconductor manufacturers in India has never stopped. Applied Materials, a major American semiconductor equipment company, recently invested $50 million to establish R&D facilities in Bangalore. Applied Materials has been operating in India for 20 years and now has a team of more than 6,000 people covering product development, operations, and information technology services.
Micron, a major memory chip manufacturer, is rapidly rising in India and recently established its India Research Center in Hyderabad. Over the past three years, the number of Micron employees in India has increased to 3,500, with the goal of reaching 5,000 employees in the next few years.
In recent years, India has intended to join the global chip manufacturing race. In December 2021, the Indian government launched a $76 billion incentive plan to attract international semiconductor and display manufacturers, aiming to make the country a global chip manufacturing center. India does have some advantages in chip manufacturing. According to the Indian Minister of IT and Electronics, India has nearly 55,000 semiconductor design engineers working for different companies, accounting for 20% of the global chip designers. Moreover, India is developing into the world's second-largest consumer market, with a value of $27.2 billion in 2021, which is expected to reach $64 billion by 2026. This is a considerable temptation for semiconductor manufacturers.Since then, we have seen many consortiums and companies starting to march into India to establish chip factories.
On September 13, 2022, Taiwan's chip giant Foxconn Group and India's mining and manufacturing group Vedanta reached a total agreement of $19.4 billion to build a chip factory in India, mainly producing chips and displays. Foxconn Group will provide chip production technology for the joint venture, while the mining background Vedanta Group will provide funding for the project.
In May this year, the joint venture ISMC, jointly established by the Abu Dhabi Next Orbit Ventures Fund and the Israeli chip manufacturer Tower Semiconductor, signed a $3 billion agreement with the Indian state of Karnataka, planning to build a semiconductor chip factory in the state. In July, IGSS Ventures, headquartered in Singapore, said it would invest $3.25 billion to build a semiconductor high-tech park in the Indian state of Tamil Nadu, including a wafer factory.
In February this year, Intel announced the acquisition of the Israeli chip manufacturer Tower Semiconductor for $5.4 billion to gain more specialized production capacity. This acquisition will strengthen Intel's position in the global wafer foundry industry.
In addition to attracting large factories to build factories in India, India is also building its own chip factories. Sahasra Semiconductors has invested 7.5 billion Indian rupees to build a memory chip factory, which is also India's first chip factory built from scratch.
According to a report by the Indian Electronics and Semiconductor Association (IESA) in April 2022, by 2030, India may account for $85-100 billion in the global semiconductor manufacturing market of $550-600 billion.
Conclusion
Over the past few decades, Southeast Asia has entered the semiconductor manufacturing industry by attracting foreign direct investment, promoting exports, and integrating into the global value chain. Now, with the transformation of the semiconductor supply chain, Southeast Asian countries are continuing to attract a large amount of foreign investment, and the future of the Southeast Asian semiconductor ecosystem seems to be full of hope.
Comments